L’Industrie du futur, également connue sous le nom d’industrie 4.0 et définie comme étant la quatrième révolution industrielle, représente une transformation majeure dans le secteur manufacturier, et offre des perspectives prometteuses pour l’avenir de l’industrie.
Née en Allemagne, cette révolution industrielle est rendue possible grâce à l’intégration de technologies avancées telles que l’intelligence artificielle (IA), l’Internet des objets (IoT), le big data, l’apprentissage automatique (MachineLearning) et bien d’autres technologies émergentes.
En permettant une interconnexion intelligente et la digitalisation des processus industriels, l’Industrie 4.0 ouvre la voie à des améliorations significatives en termes de productivité, d’efficacité énergétique et de durabilité environnementale.
Cependant, derrière cette vision prometteuse se cachent de grands défis à relever. La mise en œuvre de cette révolution industrielle peut être entravée par des obstacles tels que des contraintes financières, des manques de compétences techniques ou encore des contraintes organisationnelles.
I] Appréhender le concept dans sa globalité
L’Industrie 4.0, marque la convergence du monde physique et digital.
La combinaison des technologies favorisent une interconnexion des informations qui permettent aux industriels des gains de temps et une maitrise plus forte de leur chaine de valeur.
L’Industrie 4.0 permet donc, une automatisation accrue des processus de production, une maintenance prédictive pour réduire les temps d’arrêt des équipements, une amélioration de la qualité des produits et une réduction des erreurs de fabrication grâce à l’utilisation d’algorithmes d’apprentissage automatique comme le Machine-Learning (ML).
De plus, l’intégration de dispositifs IoT high-tech dans les usines intelligentes permet d’accroître la productivité et d’améliorer la qualité des produits, tout en réduisant les coûts de production.
L’Industrie 4.0 n’est pas seulement une révolution technologique, mais elle a également des implications sociales, politiques et environnementales. Elle pose la question de l’emploi dans un contexte où l’automatisation prend de plus en plus de place.
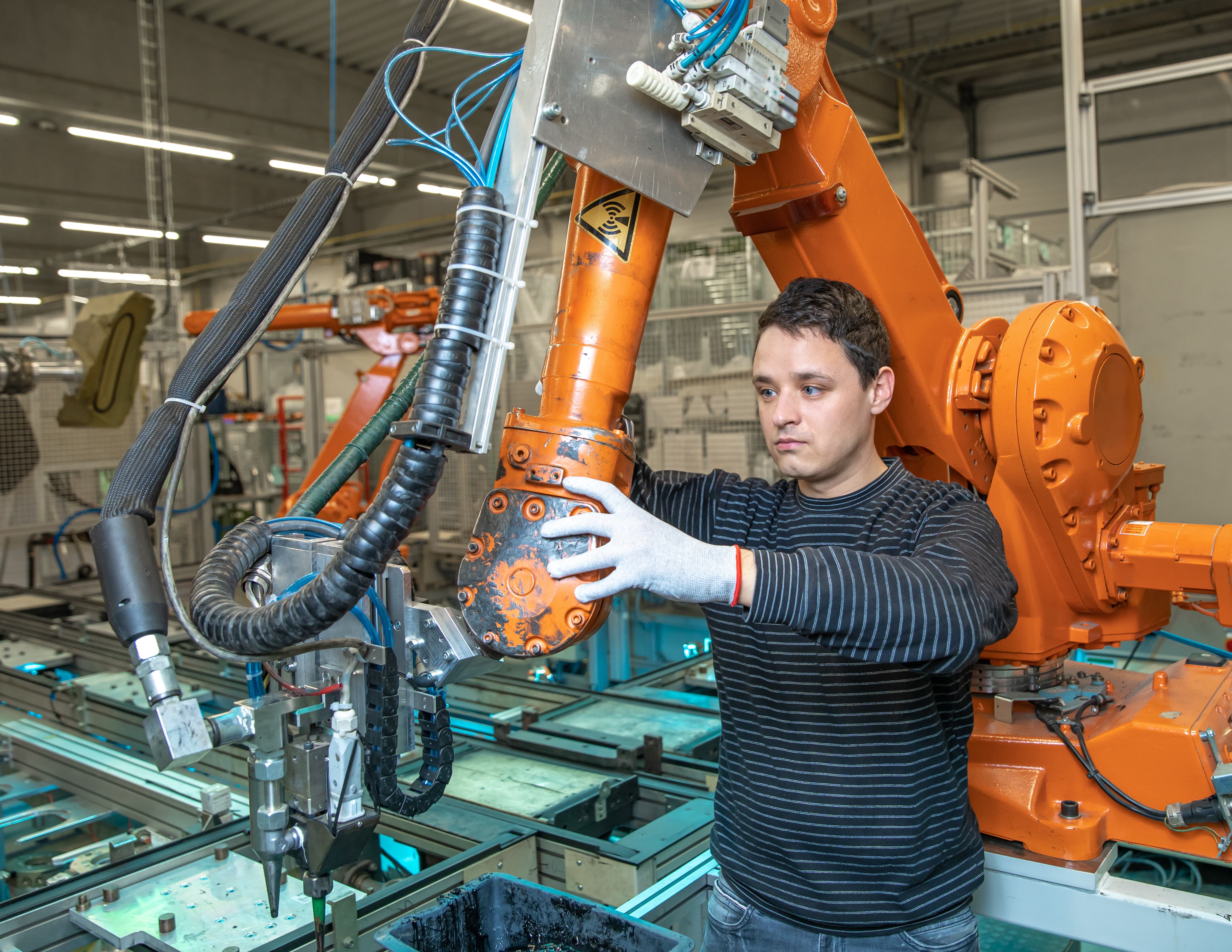
L’accompagnement des salariés actuels et la formation des futurs salariés sont des enjeux majeurs à prendre en compte dans cette transformation. Il est essentiel de réfléchir à la place de l’humain dans cette nouvelle manière de produire.
II] Intégrer la digitalisation dans la stratégie de l’entreprise
Dans l’ère de l’industrie 4.0, la digitalisation occupe une place centrale dans la stratégie de l’entreprise moderne. Après avoir appréhendé le concept global de l’industrie 4.0, il devient essentiel pour les organisations d’intégrer efficacement la digitalisation dans leur stratégie pour rester compétitives sur le marché d’aujourd’hui.
L’industrie 4.0 est caractérisée par l’interconnexion intelligente de tous les maillons de la chaîne de production grâce aux diverses technologies citées précédemment. Cela permet aux machines de produire de manière autonome grâce à un protocole Machine-to-Machine (M2M), et de s’ajuster en temps réel en fonction de la demande, améliorant ainsi l’efficacité de la production et la gestion des stocks.
Pour intégrer la digitalisation dans leur stratégie, les entreprises doivent prendre en compte les éléments suivants :
1. Définir une vision claire : La première étape pour intégrer la digitalisation dans la stratégie de l’entreprise est de définir une vision claire des objectifs à atteindre. Cela implique de comprendre comment la digitalisation peut améliorer les processus, accroître l’efficacité opérationnelle, et répondre aux attentes des clients tout en gardant à l’esprit les avantages et les défis de la transformation digitale.
2. Alignement avec les besoins du marché : L’intégration de la digitalisation doit être alignée avec les besoins du marché et les attentes des clients. Il est essentiel de comprendre comment les technologies numériques peuvent améliorer l’expérience client, accroître la réactivité aux demandes du marché et créer une proposition de valeur unique.
3. Investir dans les technologies clés : Pour intégrer efficacement la digitalisation, les entreprises doivent investir dans les technologies clés de l’industrie 4.0, telles que l’IoT, l’IA, l’analyse de données et l’automatisation. Ces technologies fournissent les outils nécessaires pour collecter et analyser les données en temps réel, optimiser les processus de production et améliorer la prise de décisions.
4. Formation et sensibilisation des employés : L’intégration de la digitalisation nécessite un changement culturel au sein de l’entreprise. Les employés doivent être sensibilisés à l’importance de la transformation digitale et formés aux nouvelles technologies pour qu’ils puissent les utiliser de manière optimale et contribuer activement à la mise en œuvre de la stratégie de digitalisation.
5. Intégration dans les processus existants : La digitalisation ne consiste pas à remplacer complètement les processus existants, mais plutôt à les améliorer en utilisant les technologies numériques pour les rendre plus efficaces et plus agiles. Il est essentiel d’intégrer la digitalisation de manière transparente dans les opérations existantes pour optimiser la productivité et minimiser les perturbations.
En intégrant efficacement la digitalisation dans leur stratégie, les entreprises peuvent alors bénéficier de nombreux avantages, tels que l’amélioration de l’efficacité opérationnelle, la personnalisation des produits, la réduction des coûts de production et une meilleure compétitivité sur le marché.
III] Former, transformer et fédérer les collaborateurs
L’émergence de l’Industrie 4.0 est une révolution sociétale qui bouleverse les modes de production, les hiérarchies d’entreprises, les compétences et les métiers. Pour assurer une transition réussie vers cette nouvelle ère industrielle, il est impératif de préparer et d’accompagner les collaborateurs face aux évolutions technologiques sans précédent.

Cela passe par la formation, la transformation des pratiques de travail, et l’adhésion des employés aux changements.
1. La formation : L’élévation des qualifications des salariés est essentielle pour anticiper et relever les défis posés par l’Industrie 4.0. Les tâches répétitives et dangereuses laisseront place à des missions de surveillance et d’amélioration des processus, exigeant des compétences spécifiques. Le numérique remodèle le travail et requiert des connaissances techniques avancées, notamment en programmation, développement web, traitement et collecte de la data et tout ce qui est inhérent aux nouvelles technologies.
2. La transformation : Le numérique ne remplace pas le travail, il le remodèle. L’organisation du travail évolue vers de nouvelles formes de coopération et d’autorégulation des équipes, exigeant plus d’autonomie et de responsabilité des salariés. Leur adhésion est essentielle, et pour cela, ils doivent être associés à la gestion des transformations, en concertation avec leurs représentants. Le changement de posture vers l’Industrie 4.0 doit s’accompagner d’une réinvention des métiers existants et de l’émergence de nouveaux métiers, nécessitant une main-d’œuvre qualifiée, compétente, et formée aux nouvelles technologies.
3. La bonne compréhension et l’adhésion des employés : Pour intégrer avec succès l’Industrie 4.0, il est essentiel que les employés comprennent les enjeux de cette transformation. La communication et la sensibilisation sont donc primordiales pour susciter l’adhésion et réduire les résistances au changement. Les entreprises doivent fournir des informations claires sur les objectifs, les avantages et les opportunités liés à l’Industrie 4.0. Cela permettra de créer un environnement propice à l’apprentissage et à l’adaptation des collaborateurs aux nouvelles technologies et méthodes de travail.
4. Optimisation de la chaîne d’approvisionnement : L’interconnexion des systèmes de production facilite également l’intégration avec les chaînes d’approvisionnement et les partenaires commerciaux. Les données en temps réel sur la production, les stocks et la demande permettent une gestion plus efficace des approvisionnements, une meilleure synchronisation des livraisons et une réduction des coûts logistiques. Cela contribue à une chaîne d’approvisionnement plus agile et plus réactive, ce qui est essentiel pour rester compétitif sur le marché mondial.
IV] Garantir l’interconnexion à tous les niveaux de production

Dans l’Industrie 4.0, garantir l’interconnexion à tous les niveaux de production est crucial pour assurer une transformation réussie des entreprises industrielles.
Cette interconnexion repose sur l’utilisation d’IoT, de l’analyse en temps réel des données, et de l’introduction de systèmes cyber-physiques. Voici les raisons pour lesquelles cette interconnexion est nécessaire :
- Amélioration de l’efficacité et de la productivité : L’interconnexion des systèmes de production permet une communication transparente et en temps réel entre les différents équipements, machines et opérateurs. Cela permet d’optimiser la coordination des processus, d’identifier rapidement les goulots d’étranglement et les problèmes de production, et de prendre des décisions éclairées pour améliorer l’efficacité globale. Les données en temps réel facilitent également la planification et la gestion de la production, ce qui permet de mieux répondre à la demande des clients et d’augmenter la productivité globale.
- Prise de décisions optimale : L’interconnexion des systèmes informatiques (SI) et des machines permet de collecter une quantité massive de données provenant de différentes sources. Ces données sont ensuite analysées en temps réel grâce à l’IoT et au Big Data, ce qui permet de générer des informations précieuses pour la prise de décisions. Les dirigeants peuvent ainsi avoir une vision globale de la production, identifier les tendances, anticiper les problèmes potentiels, et prendre des décisions basées sur des données fiables et actualisées. Cela contribue à une meilleure réactivité et à une gestion plus efficace de la production.
- Personnalisation et flexibilité accrues : L’interconnexion à tous les niveaux de production permet de créer des lignes de production plus flexibles et adaptables. Grâce à l’analyse en temps réel des données clients, les entreprises peuvent mieux comprendre les préférences et les besoins des consommateurs. Cela leur permet de personnaliser davantage les produits et les services pour répondre aux demandes spécifiques du marché. La flexibilité accrue dans la production permet également de s’adapter rapidement aux changements de la demande et d’introduire de nouveaux produits plus rapidement.
- Optimisation de la chaîne d’approvisionnement : L’interconnexion des systèmes de production facilite également l’intégration avec les chaînes d’approvisionnement et les partenaires commerciaux. Les données en temps réel sur la production, les stocks et la demande permettent une gestion plus efficace des approvisionnements, une meilleure synchronisation des livraisons et une réduction des coûts logistiques. Cela contribue à une chaîne d’approvisionnement plus agile et plus réactive, ce qui est essentiel pour rester compétitif sur le marché mondial.
V] Gérer et traiter la data en temps réel
Dans le contexte de l’industrie 4.0, l’interconnexion à tous les niveaux de production revêt une importance cruciale pour réaliser les bénéfices complets de cette quatrième révolution industrielle. Cependant, une interconnexion réussie ne peut être atteinte sans une gestion efficace et un traitement agile des données en temps réel.
En effet, la mise en place de l’industrie 4.0 dans une entreprise exige une infrastructure solide pour collecter, gérer et analyser les données générées à chaque étape du processus de production.
La gestion et le traitement de la data en temps réel sont des éléments essentiels pour garantir le bon fonctionnement de l’industrie 4.0 au sein d’une entreprise.
Voici pourquoi cette étape est cruciale :
1. Optimisation des processus : La collecte et l’analyse en temps réel des données provenant de capteurs, de machines et de systèmes au sein de l’usine permettent une compréhension approfondie des opérations. Cela permet d’identifier les inefficacités, les goulots d’étranglement et les opportunités d’optimisation des processus de production. En ajustant les paramètres de production en temps réel en fonction des données en cours, les entreprises peuvent améliorer l’efficacité, réduire les temps d’arrêt et minimiser les pertes.
2. Maintenance prédictive : Grâce à la surveillance en temps réel des équipements et des machines, les données collectées permettent de prédire les besoins de maintenance. Les modèles d’analyse peuvent anticiper les pannes potentielles en détectant des schémas anormaux dans les données. Cela permet de planifier la maintenance de manière proactive, d’éviter les arrêts imprévus et de maximiser la disponibilité des équipements.
3. Personnalisation de la production : La capacité de collecter et d’analyser rapidement les données en temps réel permet aux entreprises de répondre aux demandes changeantes des clients et de personnaliser la production. En ajustant les paramètres de production en fonction des spécifications individuelles, les entreprises peuvent fournir des produits sur mesure tout en maintenant une production efficace.
4. Amélioration de la qualité : L’analyse en temps réel des données de production permet de détecter rapidement les variations de qualité et d’identifier les défauts potentiels. Cela permet aux entreprises d’intervenir immédiatement pour corriger les problèmes, réduisant ainsi les rebuts et améliorant la qualité globale des produits.
5. Prise de décision informée : La disponibilité de données en temps réel permet aux décideurs de prendre des décisions éclairées et basées sur des faits. Les informations en temps réel fournissent une visibilité continue sur les performances de production, ce qui permet aux dirigeants de réagir rapidement aux défis et aux opportunités.
L’intégration réussie de l’industrie 4.0 dans une entreprise nécessite une gestion et un traitement efficaces de la data en temps réel. La capacité à collecter, analyser et exploiter les données provenant de diverses sources tout au long du processus de production est essentielle pour optimiser les opérations, améliorer la qualité, maintenir la maintenance prédictive et répondre de manière agile aux demandes du marché.
La data en temps réel constitue le cœur de l’interconnexion complète des systèmes et des opérations, permettant à l’entreprise de réaliser pleinement les avantages de la quatrième révolution industrielle.
VI] Prioriser la cyber sécurité et la protection des données
À mesure que l’industrie 4.0 continue de transformer les entreprises en les rendant plus interconnectées et numériques, la priorisation de la cybersécurité et de la protection des données devient une nécessité impérative pour garantir la réussite et la sécurité de cette transition.

L’essor de l’industrie 4.0 a conduit à une convergence sans précédent entre les systèmes informatiques (IT) et les systèmes opérationnels (OT). Cependant, cette interconnexion présente également des risques en matière de sécurité. Les infrastructures critiques, telles que les usines, les réseaux électriques et les systèmes de distribution, deviennent des cibles potentielles pour les cyberattaques et les acteurs malveillants.
Dans le contexte de l’industrie 4.0, où les données circulent en temps réel à tous les niveaux de production, la priorisation de la cyber sécurité devient cruciale pour protéger ces données contre les menaces croissantes. Les données en temps réel sont un atout précieux, mais elles deviennent également une cible privilégiée pour les cybercriminels.
Les entreprises doivent mettre en œuvre des mesures de sécurité proactives pour prévenir les cyberattaques, protéger l’intégrité des données et garantir la continuité des opérations. Cela implique la mise en place de contrôles de sécurité robustes, la gestion des identités et des accès, la surveillance continue des systèmes et la sensibilisation des employés aux meilleures pratiques en matière de sécurité informatique.
La protection des données est une préoccupation majeure dans le contexte de l’industrie 4.0.
Les entreprises collectent et traitent une quantité massive de données en temps réel pour optimiser les opérations, améliorer la qualité et prendre des décisions basées sur des analyses approfondies. Cependant, ces données sont vulnérables aux violations de sécurité, aux fuites et au vol.
La mise en place de protocoles de sécurité avancés, tels que le cryptage des données, la surveillance des accès et la gestion rigoureuse des autorisations, est essentielle pour protéger les données contre les menaces potentielles.
L’importance de la priorisation de la cybersécurité et de la protection des données s’étend au-delà de la sécurité des données. En sécurisant les interconnexions IT/OT et en protégeant les données, les entreprises contribuent également à garantir la continuité opérationnelle et la stabilité de la production. Cette stabilité est essentielle pour l’optimisation de l’outil de production.
En mettant en place des mesures de sécurité solides, les entreprises peuvent créer un environnement propice à l’innovation, à l’efficacité et à la compétitivité, tout en minimisant les risques liés aux cybermenaces.
VII] Optimiser l’outil de production

L’optimisation de l’outil de production constitue un élément essentiel de la transition vers l’industrie 4.0. Cette étape vise à maximiser l’efficacité, la flexibilité et la productivité des processus de fabrication en exploitant de manière stratégique des technologies et des concepts innovants.
Voici 10 exemples d’outils clés de l’industrie 4.0 qui contribuent à l’optimisation de l’outil de production :
- L’Internet Industriel des Objets (IIoT) : L’IIoT permet aux machines et aux équipements de surveiller, de communiquer et de partager des données en temps réel. Grâce à la collecte et à l’analyse de données provenant de capteurs et de dispositifs connectés, les fabricants peuvent optimiser les performances de leurs machines, anticiper les pannes et réduire les temps d’arrêt non planifiés.
- Le Machine Learning (ML) : L’intégration du ML dans les processus de production permet d’améliorer la prise de décision en analysant des données volumineuses et en identifiant des tendances ou des modèles. Cela peut conduire à des améliorations significatives dans la gestion de la qualité, l’optimisation des paramètres de production et la réduction des déchets.
- Les logiciels de pilotage de production (MES) : Les systèmes MES (Manufacturing Execution System) permettent de superviser et de contrôler la production en temps réel, en facilitant la planification, l’exécution et le suivi des opérations. Ces logiciels contribuent à une meilleure coordination entre les différentes étapes de production, réduisant ainsi les temps de changement de série et améliorant l’utilisation des ressources.
- Le jumeau numérique : Le concept de jumeau numérique consiste à créer une réplique virtuelle d’un objet physique, que ce soit un produit, une machine ou même une usine entière. Cela permet de simuler des scénarios de production, de tester des modifications avant leur mise en œuvre réelle et d’optimiser la conception et les processus. Ils permettent aussi d’expérimenter des scénarios d’efficacité énergétique sans perturber la production réelle.
- La Réalité Augmentée (RA) trouve de nombreuses applications dans l’industrie 4.0, y compris pour la formation des opérateurs, la maintenance assistée par ordinateur et la visualisation de données en temps réel. Elle améliore l’efficacité opérationnelle en fournissant des informations contextuelles directement aux travailleurs sur le terrain.
- Le Cloud Computing : Les services cloud offrent une infrastructure flexible pour le stockage et le traitement des données, ce qui permet aux entreprises d’accéder rapidement aux ressources nécessaires pour optimiser les opérations. Les données peuvent être partagées et analysées à partir de diverses installations, favorisant ainsi la collaboration et l’innovation.
- La robotique collaborative : Les robots collaboratifs aussi appelés cobots, travaillent en collaboration avec les humains dans un environnement de production. Ils peuvent effectuer des tâches répétitives, dangereuses ou exigeantes en termes de précision, libérant ainsi les travailleurs pour des tâches plus complexes et créatives.
- L’impression 3D : L’impression 3D révolutionne la fabrication en permettant la création de pièces complexes de manière rapide et efficace. Cette technologie offre une grande flexibilité dans la conception et la production de prototypes, de composants sur mesure et de pièces de rechange, ce qui peut contribuer à réduire les délais de production et les coûts.
- L’analyse de données avancée : L’analyse de données avancée, également connue sous le nom d’analytique industrielle, permet de tirer des informations précieuses à partir des données générées par les machines et les processus de production. En utilisant des algorithmes sophistiqués, les fabricants peuvent identifier des tendances, des anomalies et des opportunités d’optimisation, conduisant à une meilleure prise de décision et à une amélioration continue.
- Les systèmes cyber-physiques (CPS) : Les CPS sont des systèmes intégrant des composants informatiques, de communication et de contrôle avec le monde physique. Ils permettent une interaction en temps réel entre les équipements, les capteurs et les actuateurs, créant ainsi des environnements de production intelligents et réactifs. Les CPS favorisent la prise de décision automatisée et l’ajustement dynamique des processus pour optimiser les performances.
En mettant en œuvre ces outils de manière synergique, les entreprises peuvent créer des environnements de production plus agiles, adaptables et performants. L’optimisation de l’outil de production dans le cadre de l’industrie 4.0 permet de répondre efficacement aux défis de la compétitivité, de la personnalisation des produits et de la satisfaction client, tout en exploitant pleinement le potentiel des technologies numériques et connectées.
VIII] Améliorer l’efficacité énergétique
L’efficacité énergétique joue un rôle crucial dans le contexte de l’industrie 4.0, où les données jouent un rôle essentiel dans la transformation et l’optimisation des opérations industrielles.

Les entreprises industrielles sont confrontées au défi de réduire leur consommation énergétique tout en maintenant des niveaux de production élevés et en respectant les objectifs environnementaux. Heureusement, les avancées de l’industrie 4.0 offrent de nouvelles opportunités pour améliorer l’efficacité énergétique de manière significative.
L’utilisation de données massives collectées à partir de capteurs et d’appareils connectés est au cœur de cette transformation. Les données sont recueillies en temps réel, interprétées à l’aide d’outils d’analyse avancés et intégrées dans des modèles prédictifs. Cela permet d’identifier les goulots d’étranglement et les inefficacités dans les processus de production, et d’apporter des ajustements pour minimiser la consommation d’énergie.
Les avantages de cette approche sont multiples, et en voici quelques exemples :
- La détection des processus inefficaces : Les données permettent d’identifier les processus de production qui consomment une quantité disproportionnée d’énergie par rapport aux résultats obtenus. En comprenant mieux ces goulots d’étranglement énergétiques, les entreprises peuvent apporter des améliorations ciblées pour réduire leur consommation.
- L’optimisation de la production et de la logistique : Les données en temps réel permettent aux entreprises de surveiller et d’optimiser la production en fonction des variations de la demande, des conditions environnementales et des coûts énergétiques. Cela peut impliquer des ajustements dans la planification, la logistique et l’utilisation des ressources pour minimiser la consommation d’énergie.
- La maintenance prédictive : Les données peuvent être utilisées pour anticiper les besoins de maintenance des équipements. En prévoyant les pannes potentielles, les entreprises peuvent éviter les temps d’arrêt non planifiés, ce qui contribue à une utilisation plus efficace de l’énergie.
- Gestion dynamique de la demande : Les données permettent d’ajuster la demande d’énergie en fonction des fluctuations des prix et de la disponibilité de l’électricité. Cela peut impliquer le décalage des processus énergivores vers des périodes où l’énergie est moins chère et plus abondante.
- L’optimisation de la consommation d’énergie et de matières premières : L’industrie 4.0 offre la possibilité de disposer d’une vision globale de l’usine et de ses équipements grâce à l’interconnexion des systèmes. Cette visibilité permet une meilleure gestion et optimisation de la consommation d’énergie et de matières premières. Les entreprises peuvent ajuster les processus de production en temps réel pour maximiser l’efficacité énergétique et minimiser les pertes. Cette optimisation intelligente des ressources contribue à réduire les coûts et à atténuer l’impact environnemental de la production.
- L’optimisation de la logistique : L’industrie 4.0 permet une meilleure gestion de la logistique grâce à l’interconnexion de tous les maillons de la chaîne de production, rendue possible par l’IoT. Les algorithmes peuvent calculer les itinéraires de livraison optimaux pour éviter les encombrements, les interruptions et les retards, améliorant ainsi le flux des marchandises. Cette optimisation de la logistique contribue à réduire les inefficacités, à diminuer les temps d’attente et à minimiser la consommation d’énergie associée au transport et à la distribution des produits.
En adoptant ces approches centrées sur les données, les entreprises industrielles peuvent réduire considérablement leur consommation énergétique tout en améliorant leur efficacité opérationnelle. Cette évolution vers une gestion énergétique plus intelligente et efficiente est un exemple concret de la manière dont l’industrie 4.0 transforme la manière dont les entreprises abordent les défis énergétiques et environnementaux.
L’Industrie 4.0 se profile comme une véritable révolution dans le secteur manufacturier, guidée par l’adoption stratégique des technologies numériques, de l’automatisation avancée et de la connectivité intelligente. Cette transformation a été caractérisée par l’intégration de l’internet et du numérique dans les processus de production et de gestion.
L’efficacité énergétique est l’un des avantages majeurs de l’Industrie 4.0, permettant aux entreprises de réduire leur consommation énergétique, de minimiser leur empreinte carbone et de contribuer à la lutte contre le changement climatique. Grâce à l’analyse de données en temps réel, à la maintenance prédictive et à l’optimisation des ressources, les entreprises peuvent améliorer leurs performances opérationnelles tout en réduisant leur impact environnemental.
Cependant, alors que l’Industrie 4.0 continue de prendre forme, de nouvelles perspectives émergent à l’horizon. L’Industrie 5.0 se dessine déjà comme une évolution encore plus profonde, introduisant le concept de collaboration renforcée entre l’homme et la machine.
Alors que la quatrième révolution industrielle a marqué le début de l’automatisation et de la numérisation, la cinquième révolution va plus loin en intégrant les capacités uniques de l’humain, telles que la créativité, la pensée critique et l’adaptabilité.
L’Industrie 5.0 place les travailleurs au cœur du processus de production, les considérant non seulement comme une ressource, mais comme un investissement précieux.
La technologie est perçue comme un outil pour améliorer et soutenir le travail humain, plutôt que de le remplacer.
En regardant vers l’avenir, l’Industrie 5.0 ouvre la voie à une nouvelle ère de collaboration homme-machine et de progrès industriel. Elle offre la promesse d’une symbiose renforcée entre la technologie et l’humain, créant ainsi un potentiel illimité pour des avancées significatives dans les domaines de la production, de l’efficacité énergétique et de la durabilité.